连续纤维增强热塑性树脂代替传统的金属基材料,可以说是当前汽车轻量化巿场关注的最热技术。从K2013年展会来看,不下10家公司展出针对这一技术的解决方案。
采用朗盛子公司Bond-Laminates有限公司的TEPEXdynalite102-RG600(2)/47%-1.0mm,由连续长玻璃纤维增强的热塑性复合材料制造的座椅壳体,首次应用于OpelAstraOPC车型,所用材料使这种座椅壳体具有极高的刚度和强度,在发生碰撞时可以吸收大量的能量,因而大幅提高了安全性。Bond-Laminates公司总经理ChristianObermann博士说:“新产品的重量要比以前的产品约轻800g,而其性能可轻易胜出由钢板和长玻璃纤维增强塑料制造的同等结构的产品。”
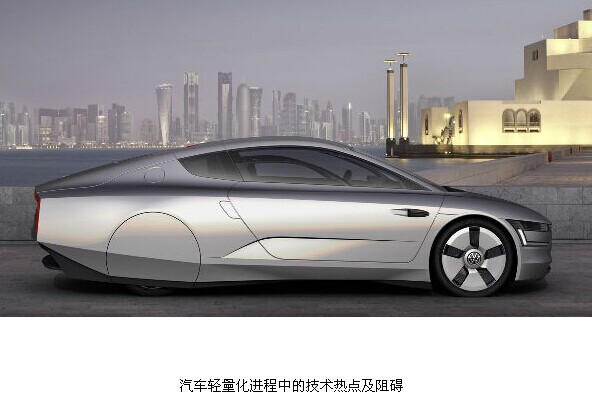
朗盛公司预计采用TEPEX的复合材料产品的需求将会增长。Obermann说:“我们发现在其他要求具有优异负载能力的汽车结构部件中也具有巨大的应用潜力,如制动踏板,安全气囊壳体,前、后座椅结构,前端载架和车底部保护部件。因此我们现在正在扩大我们Brilon生产厂的TEPEX工业生产能力。”
全球领先的玻璃增强纤维以及复合工程材料制造商欧文斯科宁借2014中国国际橡塑展之际推出其即将向中国巿场引入的专为长纤维增强热塑性聚丙烯(LFTPP)设计的PerforMax系列SE4849Type30直接纱,适用于聚丙烯树脂长玻纤造粒,连续纤维熔融浸渍,在线长玻纤增强热塑性塑料及连续纤维增强热塑性塑料片材。SE4849实现了更快的复合生产线速度,提高效率和提高玻璃纤维荷载。
连续纤维增强不只在原料企业备受关注,设备制造企业同样对这一技术给予热切的关注。领先注射技术提供商Arburg、Engel、KraussMaffei,挤出技术厂商BREYER、Milacron挤出、Reifenhäuser,压力成型技术提供商Diffenbacher,检测技术供应商IsraVision均在K2013展出针对这一技术的解决方案。
毋庸置疑,连续纤维增强技术,包括其他长纤维增强技术已成为高性能轻量化的一个重要方向。但同时,优质材料价格居高不下的价格,让轻量化的成本无疑增加许多,本土自主品牌在销量与研发资金上的短板,更使得改性塑料在汽车应用上让车企对其又爱又恨。
面对日益严格的汽车油耗法规,各大车企正在寻求多种路径降低油耗,其中就包括为车身减重。通过汽车用改性塑料量的增大,来减少车身的重量,达到降低油耗的目的。
在欧洲,汽车用改性塑料量已经成为衡量汽车设计和制造水平高低的一个重要标志,据统计,1kg改性塑料可以替代2-3kg钢等密度较大的材料,而汽车自重每下降10%,油耗可以降低6%-8%。在确保汽车整体性能的前提下,增加塑料类材料的使用量,可以有效减少整车重量,降低汽车排放,提高燃油经济性,同时降低汽车制造成本。世界上汽车塑料单车用量最大的是德国,塑料用量占材料总用量的15%。按照2005年欧洲的水平,平均单车用量已达到13%。而我国目前单车塑料用量距发达国家水平还有较大差距,有较大的提升潜力。
在我国,各大品牌开始提升合金、超强度钢、工程塑料等多种轻质化材料在汽车产品中的应用比例。今年初,福特宣布推出首款采用轻量化车身的F150,整车减重318公斤,近日又宣布旗下SUV车型探险者将成为首款采用这一轻量化设计的量产车型,随后锐界、林肯MKX等车型也将采用相关设计。但与外资品牌相比,国内自主品牌在轻量化道路上遇到了不小的挑战。由于外资材料供应商在一些核心部件方面几乎垄断了技术,自主品牌的采购价格居高不下。
部分轻质材料虽然降低重量效果明显,但是成本高昂。对于经济型产品来说,车重降低一公斤的成本控制在20元以内才是一个可接受的范围。目前在合成塑料上,相较本土材料商,外资材料商的价格平均每吨贵几千元,算下来平均每公斤增加成本几十元。
本土材料供应商的产品主要应用于保险杠、挡泥板、车轮罩等部件,在转向节、底盘悬挂等核心件的轻质化材料供应上,基本由拜耳、巴斯夫、杜邦等外资企业所“垄断”。比如拜耳的聚氨酯复合材料、聚碳酸酯塑料可以为车窗、新能源锂电池提供材料,巴斯夫的长玻纤材料则主要用于发动机悬置、车内抗冲击性组件等部件上。
政策的日益严苛,自主品牌车企在材料供应、轻量化设计等汽车产业链上的薄弱环节仍将面临严峻的考验。自主品牌企业的销量与资金相较于外资不具优势,目前以奇瑞汽车为代表的部分企业已开始联手零部件供应商、轻质化材料商以及车企三方从研发初期开始合作。
|