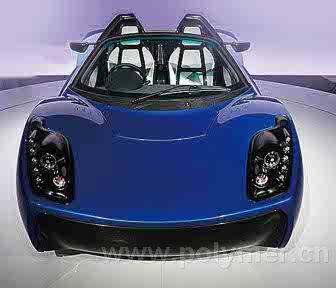
国内外汽车制造业正掀起一场革命,但都朝着高能源效率,高安全标准和高品质的设计方向发展。
汽车的普及、保有量的快速增长和城市化进程的快速实施,导致道路拥挤不堪、道路交通事故频发,噪音和废气对环境的污染等等,成为困扰人类生存环境的严重问题。人类面临着石油资源的匮乏,自然环境的破坏,生态变化的危机。因此,社会对汽车制造业提出了要求:安全、节能、环保!
高品质设计满足高标准要求
实现节省资源、环保和节能降耗的目标,必须从整车设计方面入手。从降低能耗的要求分析,可以通过:采用体积更小、品质更轻、功率更大、耗油量更低、废气排放污染更少、技术更先进的发动机;开发传动效率更高的动力传动系统;改善车身的形状;减小空气阻力;改善底盘的结构;提高整体性能。其中车身和底盘部分在汽车总品质中所占比例比较大,可改善空间大。除此之外,还必须考虑采用新型材料来降低整车的品质,从而减少燃油消耗和废气排放。
坚持高品质设计是汽车工业发展的重要途径,汽车是一个复杂的机械产品,由功能各不相同的几个基础部分、几千个零部件组成,使用的材料种类也高达上百种。所以,在设计过程中应该首先坚持轻量化、减量化,同时还必须考虑回圈经济和环保问题。
汽车轻量化,是指在保证汽车强度和安全性能的前提下,尽可能地减轻汽车的整车品质。首先要从汽车结构的合理设计开始,充分考虑到新材料(包括轻量化材料)的应用。现代汽车工业设计,几乎全部采用了CAD/CAE/CAM技术,可利用FEA有限元分析功能来分析部件结构的运动行为、应力分布,并对生成的相关资料进行工程分析与刚度和强度计算,对局部进行优化及强化设计,达到轻量化的目的。
此车共计采用了160kg的CFRP,由此将钢板用量减轻了550kg
减量化是一种颠覆传统设计理念的革命性设计手段,并不是单纯的以减轻车身品质作为最终目标,它要从结构方面考虑,本着功能集中的设计原则,尽最大可能的减少零部件的数量,减小零部件体积和外部尺寸,使结构更加紧凑;从而达到在符合各种法规和标准的前提下,在不影响整体性能的情况下,达到节能、环保、回圈经济的目的。
减量化是高品质设计中的核心组成部分,要求必须从采用全新的形状优化设计方法、先进的控制技术、轻量化车身、新型高强度轻型材料、减少零部件数量、优化结构和提高工艺方面开始。形状优化设计法,是基於生物学增长规律的设计方法,既可减少车身部件数量,又可减轻零件品质,还可延长零件的使用寿命。采用形状优化设计的车型零件数可以从400个减少到少於100个,品质减轻25~30%,最多可使装车品质降低500kg左右。由此,可看出这种设计的巨大潜力。
新型轻质材料在汽车轻量化过程中的重要性
汽车常用的轻量化材料有:高强度钢、铝镁合金、塑料及聚合物材料、树脂基复合材料、碳纤维复合材料、玻璃纤维复合材料等。虽然钢铁材料仍在结构材料中保持主导地位,但比例逐年下降,铝镁合金、工程塑料、复合材料等材料比例逐渐增加。“以塑代钢”已成为汽车工业发展的趋势,可以做到从汽车结构件扩展到整个汽车的内外饰件。从结构材料和功能材料的角度以及物理性能指标等方面分析,塑料及复合材料无疑是最佳的汽车轻量化材料,也是实现轻量化的重要途径之一。
塑料在汽车上的应用
塑料是汽车上应用最广泛的轻质材料。它是以合成树脂为基体,加入不同的添加剂并在一定的温度、压力的作用下,塑造成各种形状制品的高分子材料。塑料的种类繁多,按热性能分为热固性和热塑性两类;按应用范围又可分为通用塑料、工程塑料、高性能工程塑料。塑料几乎可以应用在汽车上的所有总成,行业内习惯将它们分为内装(饰)件、外装件和功能件(其他结构件)。可以对汽车安全性、舒适性、轻量化、回收利用等的提升给予了较大的技术支援。
目前使用量最大的汽车塑料有PP(聚丙烯)、PUR(聚氨酯)、PVC(聚氯乙烯)、ABS、PA(聚醯胺或称尼龙)和PE(聚乙烯)。随着现代化塑料工业的发展,高性能工程塑料也越来越多的在汽车上应用。
工程塑料和高性能工程塑料
工程塑料是指被用做工业零件或外壳材料的工业用塑料,是强度、耐冲击性、耐热性、硬度及抗老化性均优的可作为结构材料的塑料。工程塑料的主要特性是:密度小;比强度高;化学稳定性好电绝缘性优良;耐磨,具自润滑性,可减低摩擦系数;耐热性和尺寸稳定性高;抗冲击、抗疲劳性能优良。
工程塑料除了具备这些优异的性能,还可以采用通常的塑料加工方法加工成各种制品。广泛应用於汽车上。近年来,工程塑料主要是通过增韧技术,嵌段共聚或几种聚合物混炼成为高分子共混物,以增加品种和改进性能,使其抗冲击强度更接近金属。它与通用塑料并没有明显的界线,工程塑料最常见的种类主要有:聚碳酸酯(PC)、聚甲醛(POM)、聚醯胺(PA,俗称尼龙)、热塑料性聚酯(PET、PBT)改性聚苯醚(PPO)等。
特种工程塑料是指综合性能更高,长期使用温度在150℃以上的工程塑料。它具有:化学性能稳定,自润滑性能良好,硬度、强度和比强度高,阻燃性、电绝缘性和尺寸稳定性好,相对密度和导热系数小,品质轻,可塑性、材料性能适应性强,耐油、减震、隔音效果出色等优异的性能,并且成本相对比金属材料低等特点,未来在汽车上的应用会非常广泛。
高性能工程塑料有:聚醯亚胺(PI)、聚醚碸(PES)、聚碸(PSU)、聚氨酯(PU)。
塑料在汽车制造上已经具有50多年的应用历史,汽车塑料的用量是衡量一个国家汽车生产技术水准的标志之一。从20世纪70年代开始,汽车塑料的应用在从内饰件向外部饰件逐步扩展的发展历程。大量使用塑料制品,以替代各种昂贵的有色金属和合金材料,既可提高汽车造型的美观与设计的灵活性,降低零部件加工、装配与维修的费用,又可以降低汽车的能耗。在欧洲,车用塑料的重量占汽车自重的20%,而每辆德国车平均使用塑料接近300kg,占汽车总重量的22%。塑料在汽车上的应用数量日益增加,特别汽车内饰件对材料提出了更高的要求。利用塑料的质轻、防、吸振、设计自由度大的特点,现代汽车用塑料结构件取得了长足的发展,并且是今後的重点发展方向之一。
汽车工业发展前景和对塑料行业的影响
无论国内还是国外,汽车都是发展最快的工业行业之一,行业整体经济效益指标呈现“井喷式”增长。汽车工业的迅速发展,拉动了汽车制造材料的旺盛需求,直接刺激了塑料工业的发展速度,塑料在汽车制造业中扮演着越来越重要的角色。
消费者对汽车塑料应用需求
内饰材料异味已引起消费者的广泛关注,有无异常气味已成为消费者购买汽车的一个重要参考依据。国家《乘用车内空气品质评价指南》的推出,塑料产品的环保性能将面临较大的挑战,但是,很多国内的汽车公司已经开始针对汽车车内材料、安装工艺的环保问题进行专题研究。鉴於国际知名汽车主机厂针对汽车内饰件所使用的材料都有严格的气味、挥发性气体的测试标准,并且这些标准随着消费者需求的提升而变得越来越严格。
汽车的普及,消费者对於汽车有了更深入的了解,人性化、舒适性及安全性的要求也在与时共进,轻盈、节能、美观、安全、环保成为时尚。由於塑料制品具有良好的性能、低廉的价格、多彩的颜色搭配,简单的加工工艺,无疑能在满足人们对汽车的要求中大有作为。
汽车塑料使用比例日益加大
在汽车工业领域大量使用塑料制品,以代替各种昂贵的有色金属和合金材料,不仅可提高汽车造型的美观与设计的灵活性,降低零部件加工、装配与维修的费用,而且还可以降低汽车的能耗。塑料制品的用量反映了一个国家汽车工业的发展水准,德国每辆汽车平均使用的塑料制品已接近300kg,占汽车所用材料的22%左右,是世界上采用汽车塑料零部件最多的国家。日本每辆汽车平均使用塑料也达到了150kg左右,约占汽车材料消费总量的12%;甚至有一家日本公司开发销售的新型汽车,除座椅外,车顶、装潢材料、仪表盘等内饰件全部采用塑料制造。目前,汽车塑料制品应用的趋势由普通装饰件发展到结构件、功能,因而塑料原料的使用也由普通塑料(多用於汽车内饰件)扩展到强度更高、冲击性更好的复合材料或塑料合金。
世界汽车塑料的发展趋势
从现代汽车工业发展的趋势来看,对於材料性能的要求在不断提高,而由此得出结论:结构材料技术也正在向高强度、高刚度、高韧性、耐高温、耐腐蚀、高弹、高阻尼等性能大幅度提高的方向发展。高性能结构材料的不断出现和广泛应用,将会有力地促进新产品向体积小、重量轻、资源省、低能耗、低成本、高效率、高利润的方向发展。
目前,国外当前研究的方向有以汽车热塑性塑料复合材料为主要课题之一。树脂材料研究的重点是不断提高材料的物理、力学性能;材料开发已从昂贵的特殊专用树脂转向低成本的普通树脂新品种体系;自增强树脂也是当前材料研发的一大热点(如SR-PP),欧洲重点放在连续层压成形和模压成形材料上,而北美关注的是注塑成型材料。
纳米复合材料的研究和开发受到广泛关注,主要有纳米层状二氧化矽、纳米碳管来增强PA、PE、PVC,介面特性改善等等。纳米增强纤维复合材料是目前新近兴起的一种纳米复合材料。欧洲目前正在研究利用纳米碳管作增强体,开发阻燃、自增强SR-PP等高性能复合材料,如聚合物、钢纤维等其他类型的增强体也受到关注。
出於环保的需要,天然纤维增强热塑性复合材料也是当前世界各国汽车塑料的一个重要研究领域。
近年来,日本各大汽车厂商、材料生产商、相关研究机构和汽车部件厂商投入了大量的人力和资金,用於新型材料的研发。经常在国际展览会上展示能够大幅减轻重量的部件、新材料和新技术。他们基本上都是通过改变①材料、②形状、③加工方法这三个途径,减轻零部件品质。今年则提出了改用树脂和泡沫等材料,在维持刚性的同时削减多余厚度,通过改进模具和思考新接合法节省现有部件的技术。
日本东丽开发出了在车辆骨架等部分采用碳纤维强化树脂(CFRP)大幅减轻了车重的电动汽车(EV)概念车“TEEWAVEAR1”。TEEWAVEAR1概念车为可上路行驶的车辆配置,各部件在制造时非常注重实用化。该车共计采用了160kg的CFRP,由此将钢板用量减轻了550kg,是“适合量产的为热可塑性树脂”,该公司的目标是“在汽车设计领域掀起一场革命”。东丽公司将碳纤维定位为“战略性扩大业务”,汽车是最有望大量应用这种材料的领域。计画通过概念车扩大汽车厂商对碳纤维的应用。
日本帝人公司开发出了采用热可塑性树脂,用1分钟时间便可成型CFRP(碳纤维强化树脂)车辆骨架部件的量产技术,并公开了采用该技术制造的车体骨架。用CFRP成型的车体骨架为轻型车尺寸,重量降低到了采用钢板时的约1/5,即47kg。部件个数为20多个。确保了骨架所必需的碰撞安全性及刚性。由於车辆地板下部确保了足够的刚性,因而省去了中柱。帝人公司与美国通用汽车公司(GM)签署了合作开发用於量产车的热可塑性CFRP(CarbonFiberReinforcedPlastics,碳纤维强化塑料)部材产品的协定。
CFRP(碳纤维复合材料)与钢板及铝合金相比,虽可大幅减轻重量,但因为成本高,此前只被用在赛车及超级车上。日本正在开发可快速且低成本制造CFRP的技术,RTM(树脂传递模塑)成型工艺,RTM工艺可使高强度高刚性的热塑性CFRP快速成型。通过成型後再向模具中注入树脂,以及在强化纤维中不使用纺织品的改进措施,来降低成本。采用该工艺每月可生产数千个CFRP部件,成型品的成本也有望降至原来的1/5~1/7。另外,使用原来的预浸料也可在5~10分钟内成型的技术也已诞生。
美国和德国是最重视环保和废气排放的,也是高分子工程塑料在汽车上应用最多和研究最深入的国家。德国戴姆勒(Daimler)与德国巴斯夫公司(BASF)在法兰克福车展(IAA2011,)上展出了共同开发的概念车“SmartForvision”。车轮采用树脂制造,与采用金属制造相比,每个轮子的重量减轻了3kg。簧下品质的减轻对於提高乘坐舒适性和(燃油经济性)有着重要的意义。
它的驾驶室骨架由CFRP(碳纤维强化树脂)制造,基体(Matrix)是环氧树脂。重量比钢制减轻了一半。而且,座椅骨架为树脂一体成形,采用了可集中加热中间部分和腰部的座椅加热器等,从而减轻了座椅的重量。据称通过加长玻璃纤维增强PA(聚醯胺)的强化纤维而增大了强度。强度和耐久性均达到了可应用于量产车的水准。
虽然目前汽车新型材料技术水准已经有了质的提高,但是,新材料技术研发必须解决以下问题,才有可能推动在汽车上的应用:
1、减少材料的种类:目前汽车上使用的材料(尤其是由高分子材料组成的塑料)高达上百种,材料生产工艺不同,通用性较差,不利於回收和回圈再利用。
2、可回收再利用性:因为在汽车上大约有1/4的材料无法回收和再利用;其中:橡胶占1/3、塑料占1/3、玻璃及纤维合占1/3。
3、低成本:制约汽车上使用新材料的重要因素就是成本,降低成本才是获得在汽车制造业通往量产的必然趋势。
4、缩短制作周期,提高生产效率:新材料(如:主要用於车身较大面积的覆盖板的高性能工程塑料、玻璃纤维增强材料和碳纤维增强材料)的加工工艺相对复杂,加工周期比传统钢制车身长。这也同样是影响和制约汽车制造业采用这些新材料的重要因素。
5、材料的安全性,应该满足无毒、对人体无副作用的要求。
6、基本满足汽车全寿命周期要求,不会出现早期材质变化和老化等现象。
我国汽车塑料的现状及发展趋势
目前,我国汽车工业进入了一个高速增长的发展阶段,汽车产销量均已超过1800万辆,居於世界第一位。在汽车产业快速增长的拉动下,一个围绕汽车相关的高增长产业群业已形成,以塑料为代表的非金属材料产业就是这个产业群之一。作为汽车上使用的重要材料,车用塑料的产值正在逐步增长,其技术发展趋势日益受到业内的高度关注。在汽车塑料技术应用上,我国已采用如:气体辅助注射成型技术、可熔型芯技术、三维和多层中空成型技术、表面处理技术等等。但国内汽车用塑料材料无论用量、品种还是成型技术,目前还都处於比较低的水准。
我国汽车塑料相关行业存在的问题主要有:自主研发能力差,只能跟在国外企业後面跑;产品水准低、缺乏竞争力;材料标准不一致、专用材料种类少;原材料品质不稳定;供需矛盾突出(需要的供应不上,供应的没有需要);成型工艺、模具制造等相关工艺、技术问题还没有得到很好的解决。不过,随着新材料及新成型技术的出现,我国汽车工业所用的塑料制品消费量呈直线上升态势。
我国的塑料原料科研开发部门、原料生产商和汽车零部件生产商,加强产学研合作,抓住机遇,瞄准汽车塑料这块“巨大的蛋糕”,加大研发深度、速度和力度,增加塑料原料的种类,尤其是开发可用作汽车功能件、结构件的品种,建立自我产品设计团队(汽车零部件),提高模具开发和制造能力,建立高水准的汽车塑料零部件专业生产厂,为汽车制造业提供更多的选择和支援。
|